I hope you enjoy reading this blog post. If you are looking for sandblasting machine solutions, feel free to contact us.
Sandblasting, also known as abrasive blasting, is a fundamental process in surface preparation, widely utilized across various industries to clean, smooth, or roughen surfaces by propelling abrasive materials under high pressure. Understanding the mechanics of a sandblaster is essential for selecting the appropriate equipment and achieving optimal results.
In this blog, we will unravel the mystery of sandblasting machines and delve into their working principles, application scenarios, and why you should choose Taisheng sandblasting machines. By analyzing the core strengths of Taisheng’s sandblasting machines, we will reveal why they are the equipment of choice for so many companies. We will also explore the driving factors behind the growing popularity of sandblasting machines in the industrial sector. Join us for an in-depth look at the appeal of sandblasting technology and the excellence of Taisheng’s sandblasting machines!
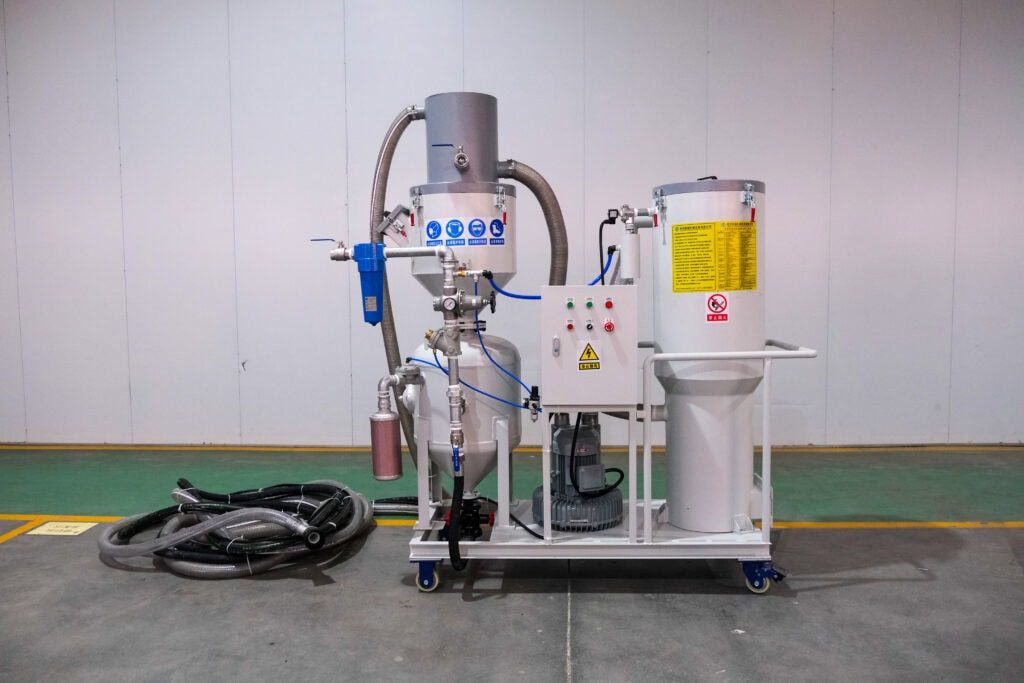
What is a Sandblaster?
A sandblaster (or sandblasting machine) is a compressed air-powered, high-speed jet beam that sprays sand at high speed into the exterior of the workpiece to be processed by a rubberized sand hose gun. The core components of a typical sandblasting system include:
●Abrasive Media Tank: Stores the chosen abrasive material, such as aluminum oxide, steel grit, or glass beads.
●Air Compressor: Generates the high-pressure air required to propel the abrasive media.
●Blast Hose and Nozzle: Directs the high-velocity abrasive stream onto the target surface.
●Dust Collection System: Captures residual dust and debris, maintaining a clean work environment and facilitating the recycling of abrasive materials.
How Does a Sandblaster Work?
The sandblasting process involves several key steps:
1. Abrasive Media Loading: The selected abrasive material is loaded into the media tank.
2. Air Compression: An air compressor pressurizes air to the required levels for effective blasting.
3 . Abrasive Flow Control: A metering valve regulates the flow of abrasive media into the blast hose, ensuring consistent delivery.
4. Surface Impact: The abrasive particles, propelled at high velocity, impact the surface to remove rust, paint, or other unwanted materials.
5. Dust & Media Collection: A dust collection system captures spent abrasive and debris, minimizing environmental contamination and allowing for the recycling of media.
What is a Sandblaster Used For?
Sandblasters are versatile tools with applications across various industries:
●Industrial Cleaning: Removing rust, paint, and coatings from metal surfaces to prepare them for further processing or finishing.
●Surface Preparation: Creating a suitable profile on surfaces before applying paints, coatings, or adhesives, ensuring better adhesion and longevity.
●Automotive Industry: Stripping old paint and corrosion from vehicle bodies and parts, facilitating restoration and repainting.
●Construction & Restoration: Cleaning and restoring brick, stone, and concrete structures by removing grime, graffiti, or old paint.
●Precision Etching: Engraving detailed designs on materials like glass, stone, or metal for artistic or functional purposes.
After understanding the basic principles and wide range of applications of sandblasting machines, you may wonder: among many brands, why does the Taisheng sandblasting machine stand out? Next, we will take you into the world of the Taisheng sand blast machine!
Types of Taisheng sand blasting machines:
Taisheng Machinery has been committed to the sandblasting machine industry for 18 years and can provide you with different types of sand-blasting machines according to your specific applications and requirements:
●Suction-Feed Sandblasters:
The suction sand blast machine is powered by compressed air, through the high-speed movement of the airflow in the gun to form a negative pressure, the abrasive is through the sand pipe into the gun and shot from the nozzle, sprayed to the surface being processed, to achieve the desired processing purpose.
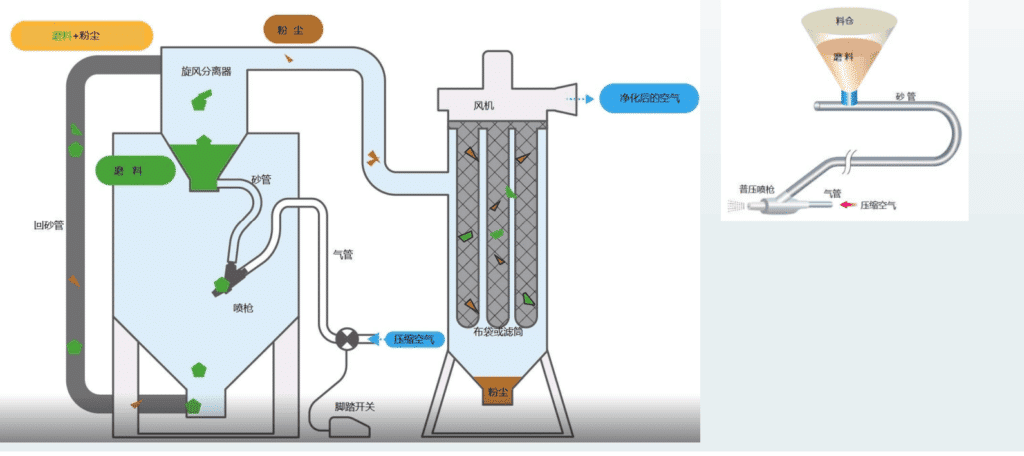
Advantages:
a. long time continuous sandblasting operation;
b. Lower cost of equipment;
c. 36-600 mesh non-metal abrasives, metal abrasives below 0.4mm can be used;
d.Low air consumption;
Weaknesses:
a. The efficiency of sandblasting is relatively low, not suitable for spraying metal abrasives larger than 0.4mm;
b.Smaller blasting distance, the best blasting distance is 50-150mm;
●Pressure Sandblasters:
The pressure sand blast machine is powered by compressed air, which builds up the working pressure in the pressure tank (also known as the sand tank). The abrasive enters the sandblast hose through the pressure of the regulated sand valve and is ejected from the nozzle at high speed to the processed surfaces to achieve the desired processing purpose.
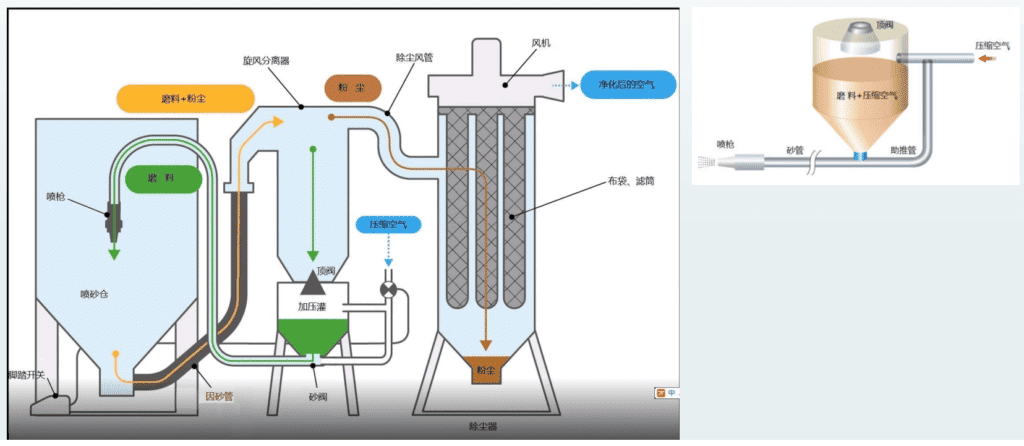
Advantages:
a.High efficiency of sandblasting;
b.Sandblasting abrasives use a wide range, 8-120, of various abrasives that can be used;
Weaknesses:
a. It is not easy to realize a long time continuous sand-blasting operation;
b.It is necessary to use a double-bin continuous pressurized sand blasting machine;
c.Not suitable for spraying abrasives finer than 120 mesh, easy to appear a pulse phenomenon;
d.Higher equipment costs;
In dry blasting, compressed air is both the power of material supply and the accelerating power of the jet. In press-in dry blasting, the time and stroke of the abrasive accelerated by compressed air are much larger than those of suction dry blasting (only in the spray gun).
●Wet Sand Blasting:
The difference between wet blasting and dry blasting is that dry blasting is not suitable for cleaning grease and dirt, while wet blasting does not have this problem.
Wet blasting is more suitable for golf ball-type workpiece surfaces that need to avoid the color difference on the surface of the material caused by the heating up of the sandblasting.
The most important feature is the use of micro-powder abrasive, wet blasting has a unique use of the effect, while the dry type has its limitations.
Generally, if the abrasive size exceeds 400#, you must consider using a wet sand blasting machine.
When the abrasive is too fine, the dry pressure blasting sand has the appearance of sand pulsation, and the production of sand and dust separation has a certain degree of difficulty, we can use the cyclone to separate to the finest grit is 600 mesh green silicon carbide, finer grit needs to be verified!
When using pressure blasting, finer than 120 mesh abrasive will have a pulsation phenomenon, using pressurized sandblasting is not recommended finer than 120# of abrasive.
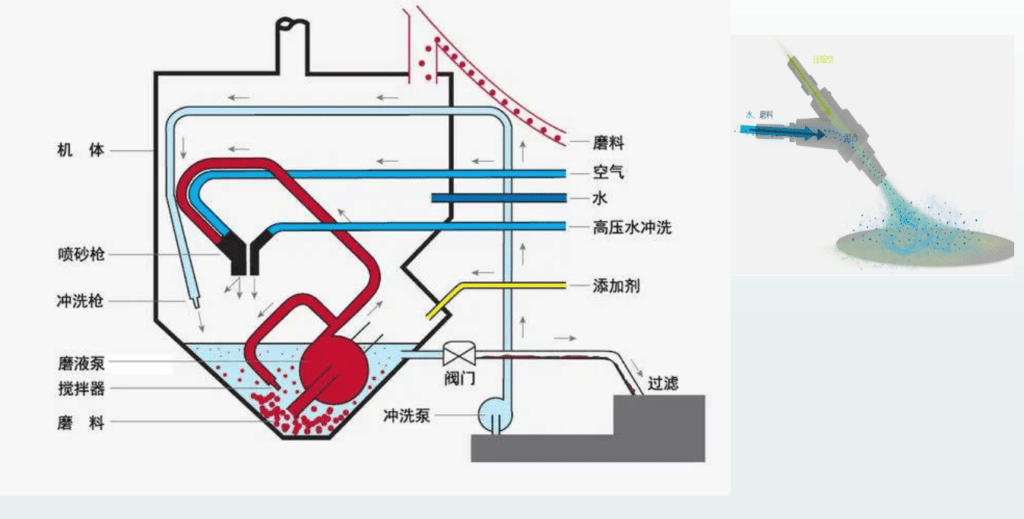
Advantages:
a. Ultra-fine abrasive can be used for surface treatment of precision workpieces(600-1200 mesh abrasive as far as possible with liquid sandblasting);
b. Clean up oil-contaminated workpieces, etc., in the case of non-filtering first de-oiled, can only use a liquid sandblasting, maintenance of automotive parts containing oil can be prioritized when choosing a liquid sand blasting machine, sand blasting liquid recycling, sand consumption is low, the nozzle wear and tear is small;
c. Good sealing, no dust pollution;
d. Simple operation, low failure rate, closed chamber, low noise;
e. The sprayed products have little damage and can be sprayed to very fine;
f. Stainless steel or fiberglass body, durable;
Weaknesses:
a. Low efficiency of sandblasting: To prevent carbon steel parts from rusting, they need to be added to the sandblasting liquid to prevent the rusting of iron workpieces;
b. Need to deal with sewage, easy to freeze in winter in the north, need to add antifreeze, the overall processing cost is higher;
Therefore, dry blasting can be used as much as possible with dry blasting.
Advantages of using Taisheng Machinery sand blasting machine:
Efficiency and Speed: Taisheng Machinery offers a wide range of types of sandblasting equipment such as drum type, suspended type, and roller pass type. These machines are designed to efficiently handle workpieces of different shapes and sizes, increasing the speed and efficiency of the blasting operation.
Cost-effectiveness: The company has specialized in the production of sandblasting equipment since 2007, with rich experience and professional design capabilities. By providing standardized and customized products, Tyson Machinery is able to meet the specific needs of customers, avoiding unnecessary expenditures and improving cost-effectiveness.
Abrasive Versatility: Taisheng Machinery’s sandblasting equipment is suitable for a wide range of abrasives, including stainless steel shot, wire cut shot, steel shot steel grit, aluminum oxide, ceramic beads, glass beads, and walnut shells. This versatility allows users to choose the right abrasive for different surface treatment requirements.
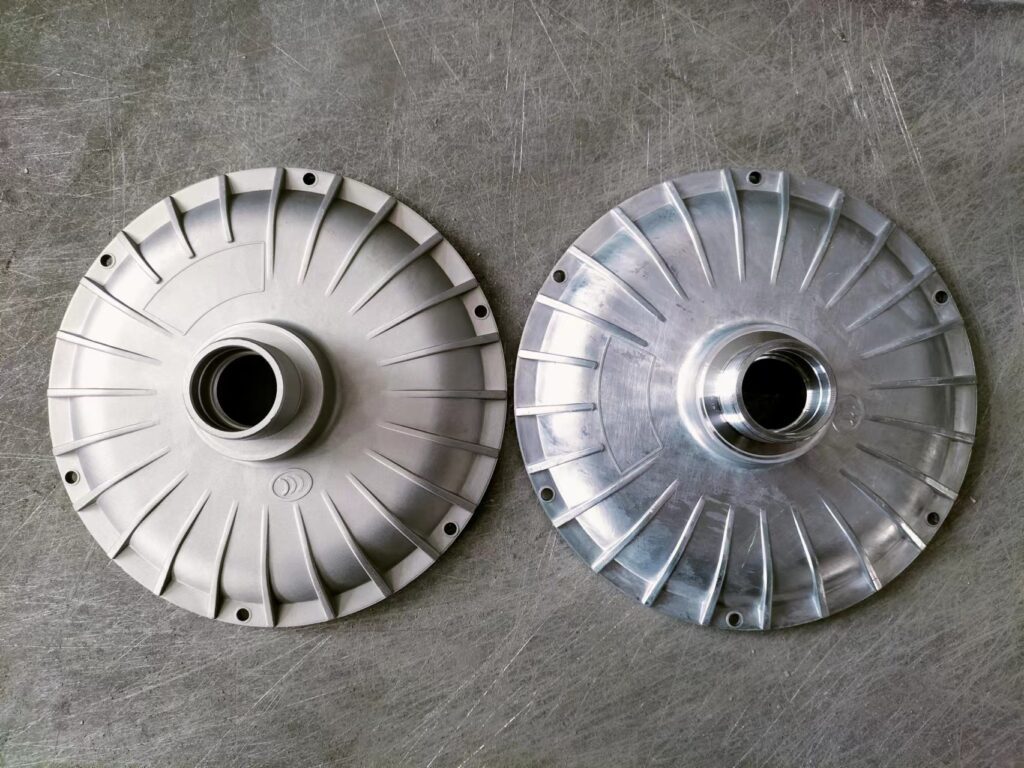
Environmentally friendly options: The company provides a sandblasting room and sandblasting equipment equipped with a dust collector, which helps to reduce dust emissions, improve the working environment, and meet the requirements of environmental protection.
Mechanical quality and after-sales service: Taisheng Machinery has strong manufacturing capabilities and a professional design team to provide high-quality sandblasting equipment. In addition, the company provides complete surface treatment solutions to ensure that customers receive comprehensive technical support and after-sales service during the process.
Conclusion
Understanding the function and application of sandblasting machines is the key to realizing the best surface treatment effect. By choosing the right equipment and abrasive media, industries can effectively solve a series of problems such as low efficiency, high labor costs, unstable surface treatment quality, dust pollution and environmental protection pressure, and difficulties in handling complex workpieces in traditional processes. This is the core reason for the popularity of sand-blasting machines.
TaiSheng Machinery has always been committed to providing innovative, reliable, and demand-driven sandblasting solutions to help various industries meet ever-changing challenges. Our team of professionals will customize the optimal solution for your specific needs, ensuring that every process achieves a superior surface finish.
Contact us today to learn how our expertise and state-of-the-art equipment can revolutionize your production process and help you achieve your goals of higher efficiency, lower cost, and better quality surface preparation!